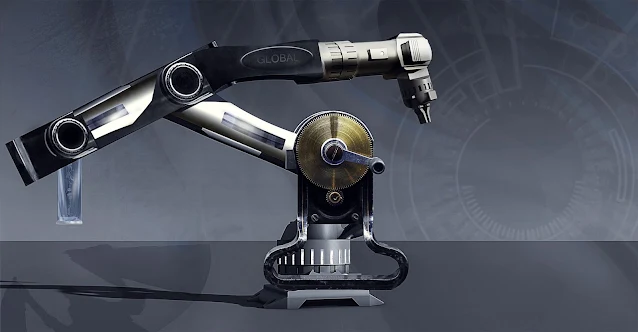 |
Source: https://pixabay.com |
Various industrial robots in use today have made their name in the manufacturing circles, like the EVS CNC robot, have transformed how assembly plants run their day-to-day operations, with most of the plants that switch to these types of robots starting to see their profits gradually rise. With robots forming a massive chunk of factory labour, it is paramount that you only work with the best; after all, the whole point of replacing human labour with robots is to improve productivity. So how do you go about choosing a robot for your factory?
The Payload
 |
Source: https://www.evsint.com/ |
A robot’s payload is the maximum load size it can carry without breaking apart. If you are running a factory with heavy loads, you may want to go for a robot that can handle the same oversized loads. Robots designed to handle heavy items cost more than smaller ones and take up more space. You will also have to pay attention to the gripper's ability to hold onto things without dropping them.
The Number of Axes
 |
Source: https://www.pinterest.com/ |
The more the number of axes, the more flexible a robot is, and as you are well aware, there is much more than a flexible robot can do compared to one limited by the number of axles. Industrial robots usually have between 2 and 6 axles, each serving a specific function. A 4-Axis robot, for example, can handle the picking and placing of leads onto a truck or a conveyer belt, something that a 2-Axis robot cannot do. A 6-Axis robot, on the other hand, can twist and turn without moving an inch. On the flip side, however, it takes a more sophisticated program to run a robot with more than 4 axles.
The Reach
Industrial robots depend on their arms to do all their operations. These arms come with grippers that enable them to take hold of the most minor things. Robots with longer arms are suitable for packaging as they can easily pick items from afar without moving. Shorter robotic arms are ideal for intricate work, like assembling computer processors that require minimal movements. When choosing a robot, consider its arm reach first to ensure it aligns with the task you have in mind.Speed and Accuracy
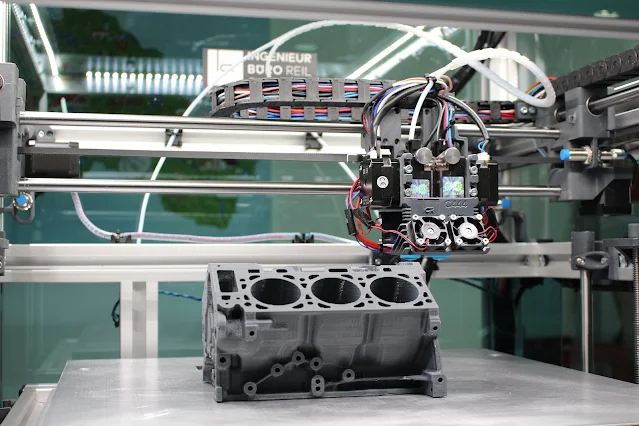 |
Source: https://pixabay.com/ |
The need for speed and accuracy are the two main reasons why many factories worldwide have chosen to replace people with robots. However, not all robots are created equal. Some are faster than others, and some are designed to deliver precision. The quicker the robot, the better it is for you, as you can complete more work within a specified time frame. When it comes to speed, however, make sure it does not come at the cost of accuracy.
Program Complexity
The best industrial robots are not just for show; they are run by some of the most complex programs ever devised by man. The advantage of using such a robot is that you are assured of the utmost accuracy with the most minuscule margins of error. The downside ofis that it will require qualified experts to run them. Therefore, when getting a robot for your plant, go for what your technician needs in case of a malfunction. The last thing you want is to stop the product so you can send the robot back to the manufacturers for repairs.Body Weight
 |
Source: https://www.pinterest.com |
Industrial robots are not light. They are made of many metal parts that combine to create one heavy machine. If the manufacturing process involves many, you should consider using more delicate types of robots. But if the work involved is serious, like car assembly, the heavy fixed robots may be the best route for you. Before buying any type of robot, make sure you have created a support system, like a guard rail, that can handle its weight.
Protection Level
The protection level is a very vital aspect of owning industrial robots. They first have to be safe to work around since some functions need human input. They should have an easy-to-access overriding button that can be switched off immediately in case of an accident. Protection from the kind of work the robots do is also vital. For instance, if the robot handles many flammable materials or acids, it should be well protected by a particular casing to avoid accidents and damage during work.
Conclusion
Technology can move forward whether people want it to or not. It is only a matter of time before every factory fully automates. As much as this will cause disruptions in the job market, there is very little that can be done to stop it. On a positive note, robots are programmed to give their everything, which means that the quality of products and services will continue increasing every day, which is something worth looking forward to.
Social Plugin