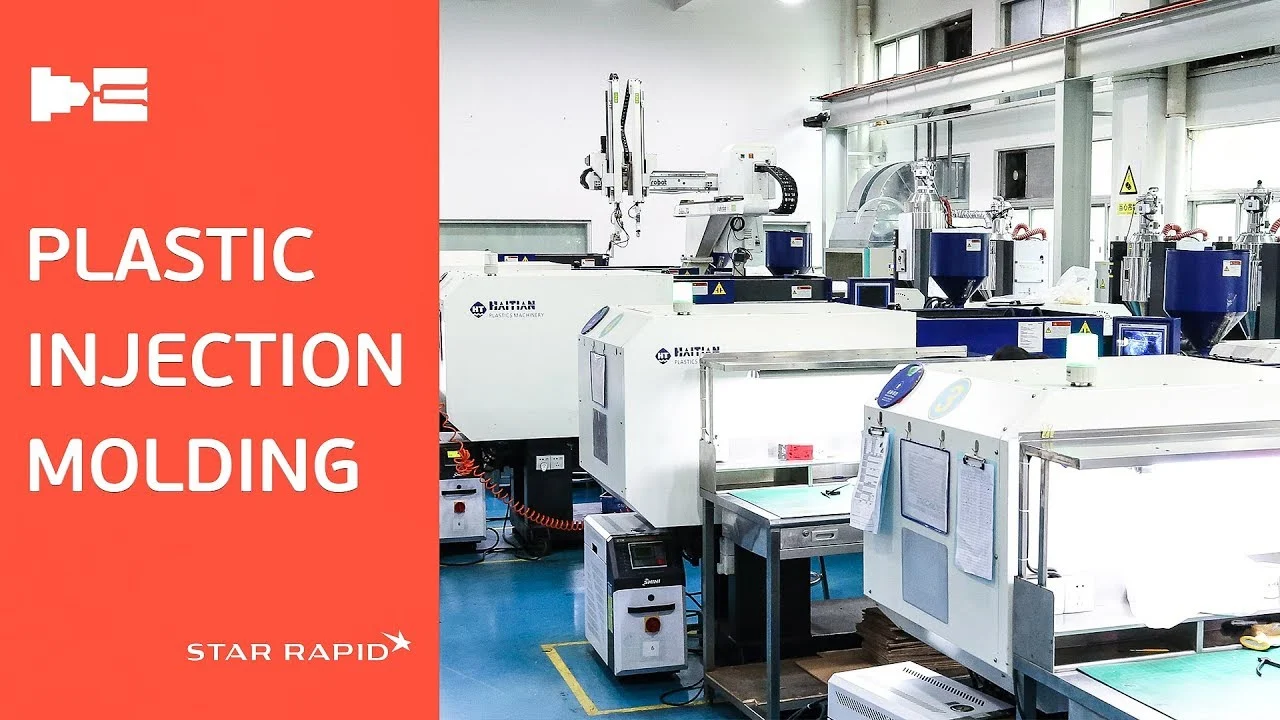
Injection molding is a commonly used process for the manufacturing & fabrication of the plastic parts. There are many items that are made with the injection molding process, and these items range greatly in application, size, and complexity. The process needs an injection molding machine, mold, and raw plastic material. The process is pretty simple as the raw plastic is melted and injected into the mold, and as it cools down and solidifies into the final product.
What are the uses of plastic injection molding?
These moldings are used to produce plastic parts that are thin-walled, and one of the common uses for these are the plastic housings. The term plastic housing defines a thin-walled enclosure that mostly requires ribs and bosses on the interior. Such housings are used in many products ranging from household appliances to dashboards of vehicles, power tools, and electronics. The other applications of these thin-walled products include many open containers and buckets etc. There are other uses of the injection molding as well as it produces many items of everyday use, including toys and toothbrushes. Even some medical items are made from the plastic injection molding process, including the syringes and valves.
What is the process of injection molding?
The cycle for the process of injection molding is pretty short and mostly lasts up to 2 minutes and has the following stages.
1. Clamping
This is before adding the material in the mold, the two halves of the mold must be placed securely by clamping units. Both halves of the mold are attached to the injection molding machine, and the other side is allowed to slide. The hydraulic power clamps push the mold in the haves and provide sufficient force to keep the molds in place while the material is added.
2. Injection
The plastic material is fed to the machine, which moves towards the injection unit, and here it is melted with pressure and heat. The melted plastic is injected into mold instantly, and the pressure packs hold the material. The material amount injected is referred to as the shot.
3. Cooling
The plastic melted inside the mold starts to cool down when it comes in touch with the interior surfaces of the mold. The plastic cools down and solidifies into the desired shape with the help of the mold. The shrinkage of the parts may occur during cooling down. The packing of material in the injection process helps the additional material to get inside of the mold, too, so the possible shrinkage chances can be reduced.
4. Ejection
When enough time has passed, the parts that are cooled are ejected from the mold by the ejection system that is attached to the rear half of the mold. When mold is opened after it is cooled down, there is a mechanism used to push the part out of the mold. There must be enough force to get the part to eject because sometimes, during the shrinkage, the plastic begins to adhere to the mold. So, to have a perfect ejection, a mold release agent is sprayed on the surface of the mold before the injection of the material.
Where can I get plastic injection molding services?
There is a highly recommended company that specializes in plastic injection molding based in China. The company is named Qmolding and can be found at
https://qmolding.com/. The company is the leader in China’s plastic injection molding industry. The company offers a range of services related to plastic molding as well as silicone and rubber molding services. Do check them out to find out more.
Social Plugin